The concept of variability in personnel management
“The manager must become a leader whose main task is to create a system that enables employees to work effectively. A necessary condition for the implementation of this role is the leader’s understanding of the differences between general and special causes of variability.”
Source: CRISIS OF THE COAL MINING INDUSTRY AND MODERN MANAGEMENT THEORY Netsvetaev Alexander Glebovich, Rubanik Yuri Timofeevich, Mikhalchenko Vadim Vladimirovich / Kemerovo, Kuzbassvuzizdat, 1998, 92 pp., ISBN 5-202-00323-4, BBK U9(2Ros)3 05.651, N 38
Color illustrations and notes: Scientific Director of the AQT Center Sergey P. Grigoryev
Free access to articles does not in any way diminish the value of the materials contained in them.
Deming wrote: “The manager must be able, by calculation, if data is available, or by judgment, when such data is not available, to distinguish those of his employees who are outside the system, both for the worse and for the better, and thus require either special assistance, or should be allocated and encouraged in one form or another.” [Deming W. E., Out of the Crisis.]
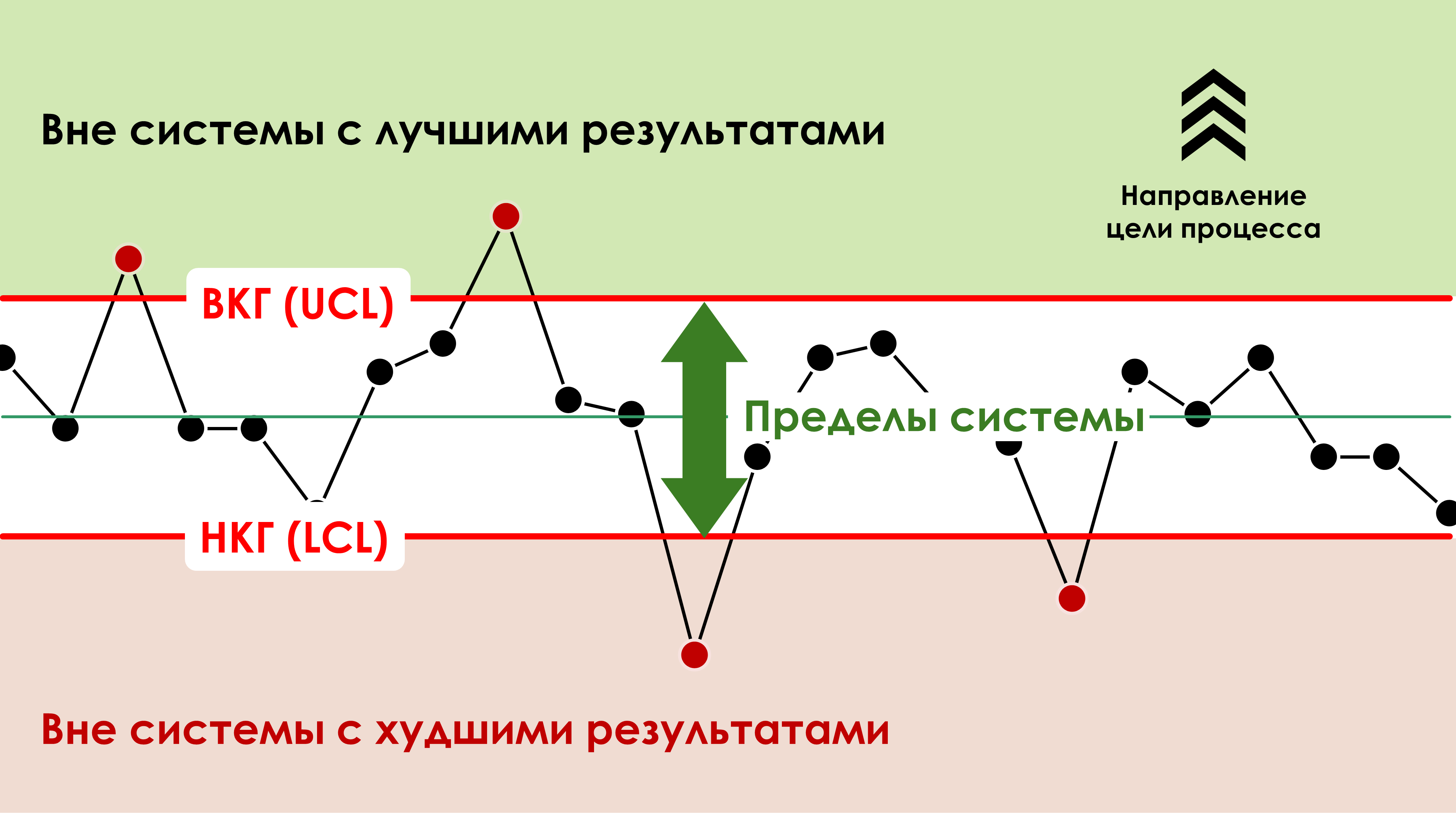
Figure 1. System limits determined by Shewhart control chart
See a detailed description of how to use control charts to work with employees working within and outside the system with the best and worst results in an open solution: Erroneous use of KPIs in the personnel motivation system
Variability in the performance of individual workers is the result of either general causes of variability or special causes. Of course, a manager must be able to distinguish between these reasons.
Myron Trybus in the article Viral theory of management gives an example of the tendency to erroneous judgments inherent in the ordinary consciousness of people who do not have an understanding of the concept of variability. The vast majority of the many dozens of Western managers he interviewed, analyzing individual differences in the number of errors made by employees (table in Figure 2), recommend “dealing with Eve,” the results of which clearly do not fit within the “average level” of work quality demonstrated by the majority of workers .
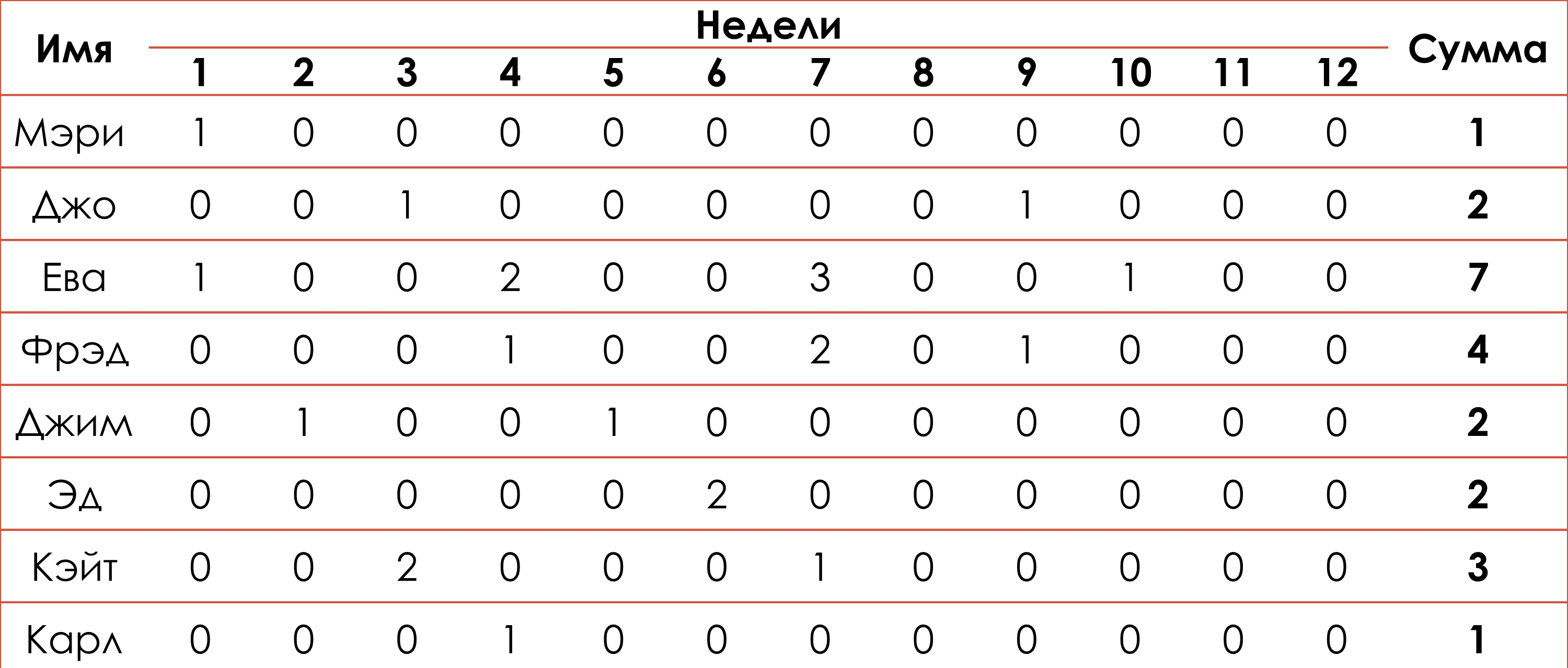
Rice. 2. Table of the frequency of production defects by employee (pcs./week).
In fact, the data presented in the table was obtained artificially, by throwing out random numbers, and thus are a manifestation of the action of factors potentially inherent in a particular system. This circumstance could be immediately detected if the appropriate type of Shewhart control chart was used (Fig. 3), which shows that individual deviations in the quality of work are entirely within the range determined by the general causes of variability.

Figure 3. Control chart C-card of the number of production defects by employee (pcs/12 weeks)
Donald Wheeler recommends not using control charts for alternative data unless you have a graduate degree in statistics. For a detailed explanation, see his article: Control charts for alternative data (counts) p-chart, np-chart, C-chart and u-chart or XmR-chart of individual values? Moreover, Edwards Deming in his book “Out of the Crisis” recommends using a statistically significant period to evaluate people’s work, for example, from eight periods (weeks, months, quarters - depending on the content) with the construction of a control XbarR-chart of average and ranges of subgroups with grouping of data by employee and subgroup size (number of periods), for example, (n=4). See the open source solution for a detailed description of this method: Erroneous use of KPIs in the personnel motivation system . - Note Sergey P. Grigoryev
In practice, misunderstanding of this circumstance manifests itself in various forms. Ranking of employees based on the results of their work, identifying “the best employees of the week, month, year,” various bonus and de-bonus schemes.
In fact, the labor results of all workers shown in the table in Figure 2 are essentially the same. These are random manifestations of the same system. Ranking these employees, rewarding the “best based on quarterly results” and depriving (or even firing) the “worst” is the same as rewarding and punishing those who won or lost the lottery. This will be another manifestation of interference in a stable system. And just as in the case of the previously discussed technical and organizational systems, such interference is fraught with aggravation of the situation. Ranking people in a situation where the results of their work are completely determined by factors external to them, over which they have no control, has an extremely destructive, demoralizing effect on the individual and the organization as a whole.
At the same time, understanding the fact that all employees who have up to 5 defects per quarter belong to the same system and should not be ranked in any way does not mean that the manager is necessarily satisfied with this frequency of occurrence of defects. Understanding the concept of variability allows you to assess where the main reserves for improving quality are located and choose the right strategy for improving it. In the case under consideration, such reserves are mainly associated not with the selection of more attentive or diligent workers, the choice of methods for stimulating labor, but almost entirely with the improvement of the system itself (changes in labor methods, selection of materials, better adjustment of technical means, etc.).
Establishing the fact that the results of a certain employee's work exceed control limits and are thus determined by the action of special causes of variability does not necessarily mean that he is personally at fault. In itself, this circumstance, in accordance with the Shewhart criterion, only means that it is economically, technically feasible and effective to try to understand the reasons for this specific, truly significant deviation.
Quite often, a careful consideration of the sources of special causes of variation reveals the effect of systemic factors. Thus, in the work [Deming W. E. Out of the Crisis], data on the number of defects made by various welding operators were considered. The control chart constructed from these data indicated that the results of one of the welders were actually significantly worse (this significance is determined by the limits of the system according to the Shewhart control chart, see Fig. 1 - Note by S.P. Grigoryev) than the others (there was a manifestation special cause of variability). Subsequent study revealed that the cause of the increased number of defects produced by this welder was due to visual impairment. After this employee was prescribed glasses, his work quality immediately returned to normal. Moreover, a subsequent examination of the vision status of all other workers showed that many of them had visual impairments, although they had not yet reached a critical level. Appropriate vision correction for all those who needed it led to an overall decrease in the level of defects in this operation. Thus, the emergence of a special reason for variability was associated with the imperfection of the management system itself - the lack of control over the state of vision of workers engaged in operations where good vision is a mandatory condition.
It is not only workers and ordinary employees who fall victim to widespread prejudices and common sense. No less often, managers suffer from similar approaches. Managers and line managers are often under stress caused by the need to achieve plans issued from above and very little taking into account the potential capabilities of the system, and even more so the level of variability inherent in it. This is especially true for organizations that use various options for “management by objectives” (planned indicators).
See article by Peter Scholtes: Management by Objectives (MBO) method, what's wrong? . - Note Sergey P. Grigoryev
If the financial or production target (plan) was not established on the basis of studying the potential capabilities of the system, taking into account its inherent variability, then the actual result achieved will correspond to the required one only randomly.
If it is less than the potential capabilities of the system, you will suffer losses due to their underutilization. But much more often it turns out that the established value of the plan significantly exceeds the real capabilities of the system: “The plan must be intense!”
When a manager or employee is faced with the need to fulfill a plan that exceeds the capabilities of the system, he is faced with a choice:
- Modify the system so that it can achieve the specified target.
- Deform, distort the system (meet volume indicators by reducing quality, ensure profit by deceiving the client, etc.).
- Falsify data.
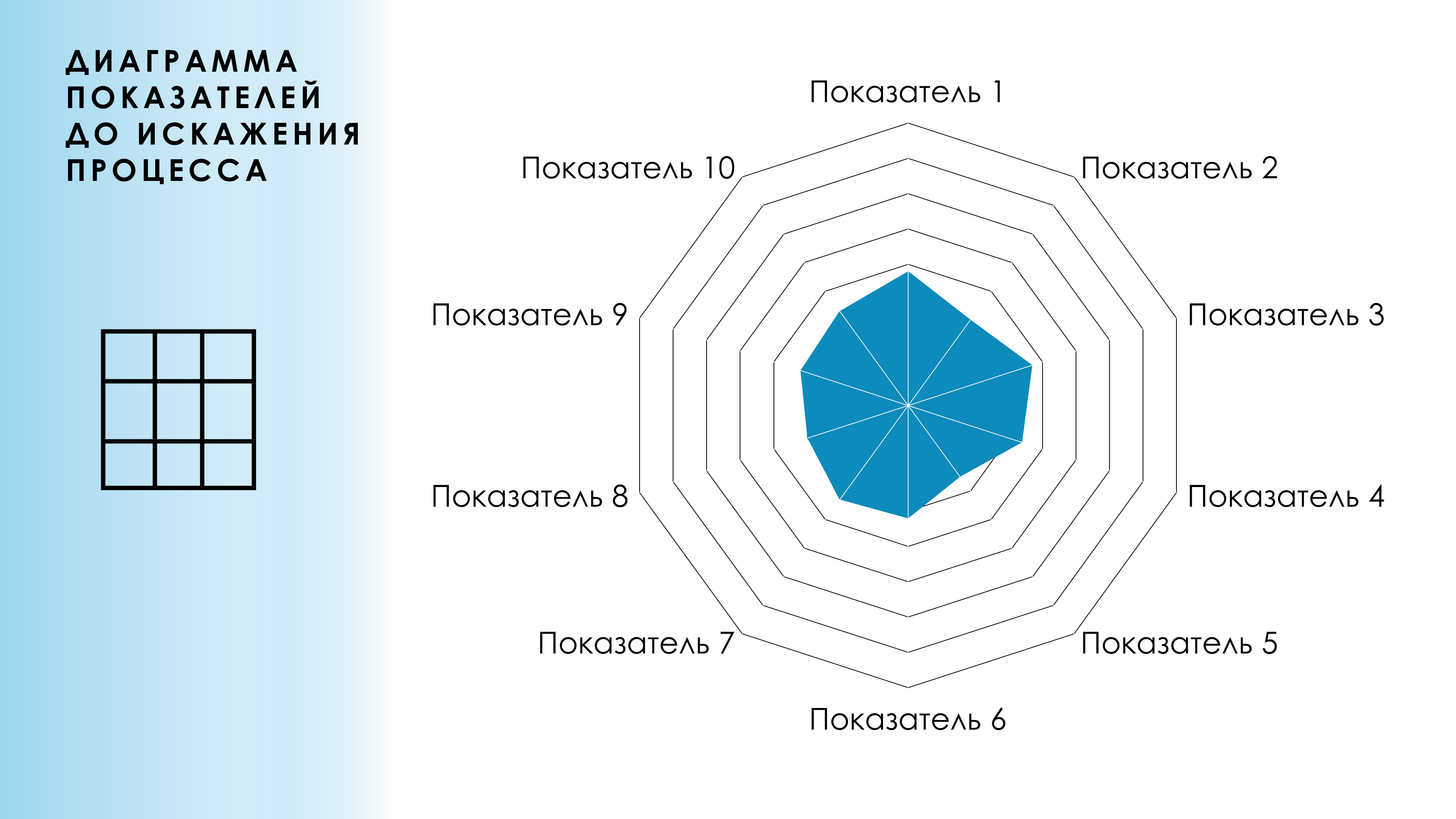
Figure 4. Radar chart of indicators before system distortion
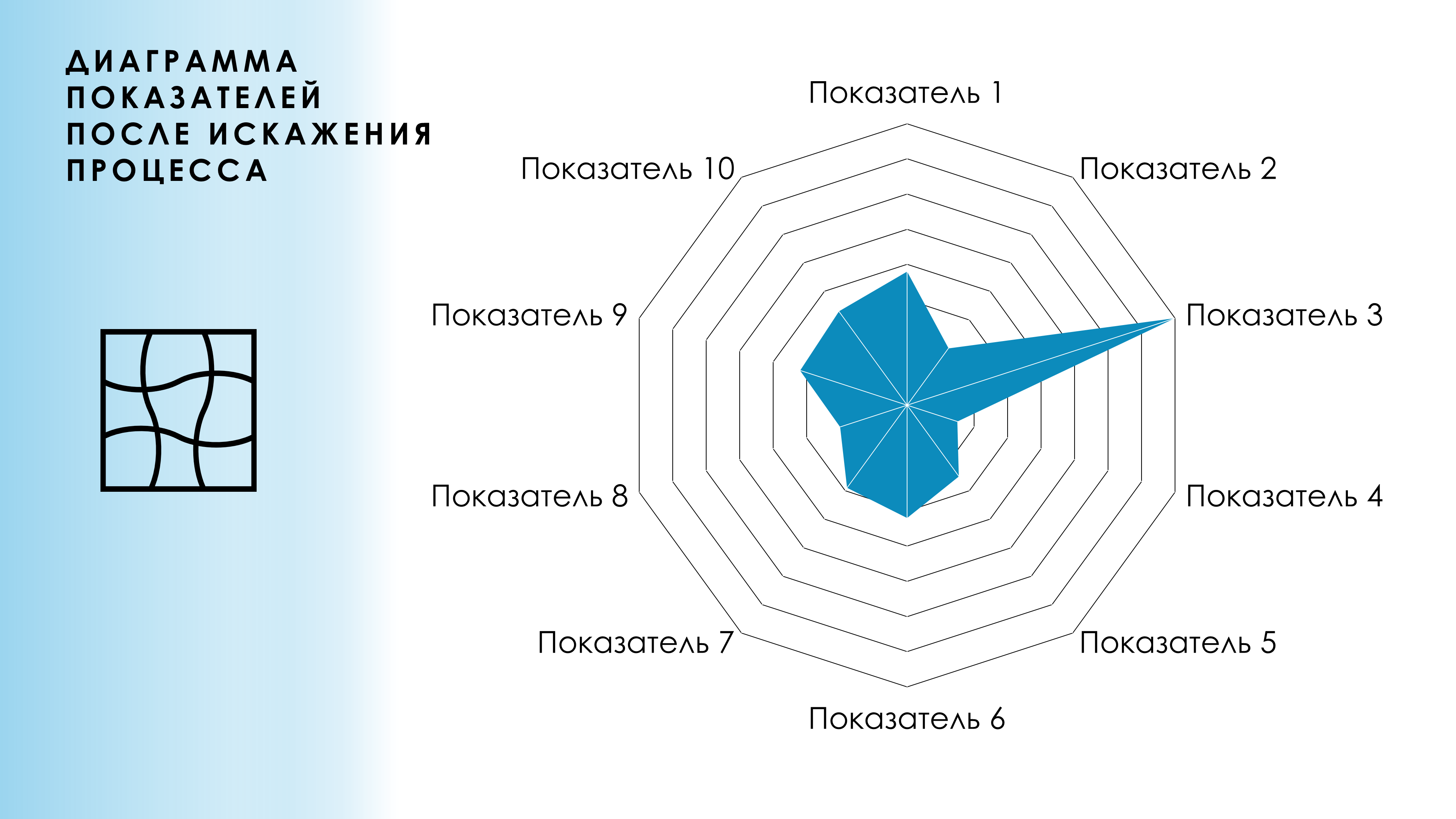
Figure 5. Radar chart of indicators after system distortion
Taking into account that changing the system is the most difficult path, requiring the investment of resources, time, and most importantly, the appropriate authority, power, it is not surprising how often in practice we encounter a variety of options corresponding to points 2 and 3 in the list possible actions. Practical managers and traditional management science have invented many techniques and systems that put barriers to the “innate depravity” of human nature. Both of them were always puzzled and admired by the inexhaustible ingenuity of workers in finding ever new ways to overcome and bypass these barriers. The eternal management problem, therefore, has always been the question: how to allow the creative abilities of people to manifest themselves in a useful direction, without allowing anarchy to triumph?
The vast majority of this kind of “eternal” problems that arise when following traditional management methods are a consequence of neglect and failure to take into account the objective laws of nature. Understanding the concept of variability gives managers the knowledge that allows them to reliably predict the reaction of both individual workers and processes, systems, and organizations to arbitrary, out-of-the-blue requirements that do not take into account the natural variability in the properties of processes and people. But most importantly, it equips managers who take the trouble to study it with an effective management strategy that significantly increases their chances of success.